1、选择要改q的关键程
_生方式不是一y而就的,它强调持l的改进。首先应该先选择关键的流E,力争把它建立成一条样板线?/span>
2、画Zh值流E图
价值流E图是一U用来描q物和信息的Ҏ。在l制完目前状态的价值流E图后,可以描绘Z个精益远景图(Future Lean Vision)。在q个q程中,更多的图标用来表Cl的程Q各U类型的拉动pȝQ均衡生产以及羃短工装更换时_生周期被细分ؓ增值时间和非增值时间?/span>
3、开展持l改q研讨会
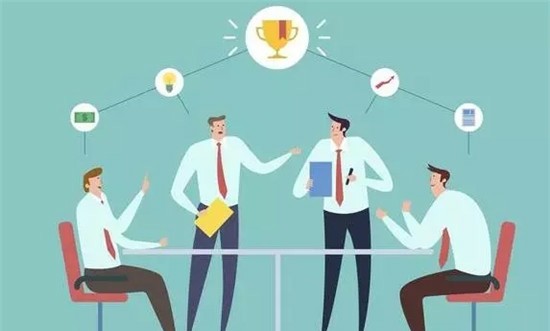
_q景囑ֿM诸实施,否则规划得再巧妙的图表也只是废纸一张。实施计划中包括什?What)Q什么时候(WhenQ和谁来负责QWhoQ,q且在实施过E中讄评审节点。这P全体员工都参与到全员生性维护系l中。在价值流E图、精益远景图的指gQ流E上的各个独立的改善目被赋予了新的意义Q员工十分明确实施该项目的意义。持l改q生产流E的Ҏ主要有以下几U:消除质量环节和q工现象Q消除零件不必要的移动;消灭库存Q合理安排生产计划;减少生准备旉Q消除停机时_提高力_利用率?/span>
4、营造企业文?/span>
虽然在R间现场发生的显著改进Q能引发随后一pd企业文化变革Q但是如果想当然地认为由于R间^面布|和生操作方式上的改进Q就能自动徏立和推进U极的文化改变,q显然是不现实的。文化的变革要比生现场的改q难度更大,两者都是必d成ƈ且是相辅相成的。许多项目的实施l验证明Q项目成功的关键是公叔RDw体力行地把生方式的改善和企业文化的演变结合v来?/span>
传统企业向精益化生方向转变Q不是单U地采用相应?ldquo;看板”工具及先q的生理
_生技术就可以完成Q而必M全体员工的理念发生改变。精益化生之所以生于日本Q而不是诞生在国Q其原因也正因ؓ两国的企业文化有相当大的不同?/span>
5、推q到整个企业
_生利用各种工业工程技术来消除费Q着g整个生程Q而不只是个别或几个工序。所以,hU的成功要推q到整个企业Q操作工序~短Q推动式生pȝ被以֮为导向的拉动式生产系l所替代?/span>
总而言之,_生是一个永无止境的_求精的过E,它致力于改进生程和流E中的每一道工序,最大可能消除h值链中一切不能增加h值的zdQ提高劳动利用率Q消灭浪费,按照֮订单生的同时也最大限度的降低库存?/span>
׃l企业向_企业的{变不可能一y而就Q需要付Z定的代hQƈ且有时候还可能出现意想不到的问题。但是,企业只要坚定不移走精益之路,大多数在6个月内,有的甚至q不?个月Q就可以收回全部攚w成本,q且享受_生带来的好处?/span>
文章来自|络Q版权归作者所有,如有侉|误pd?/span>